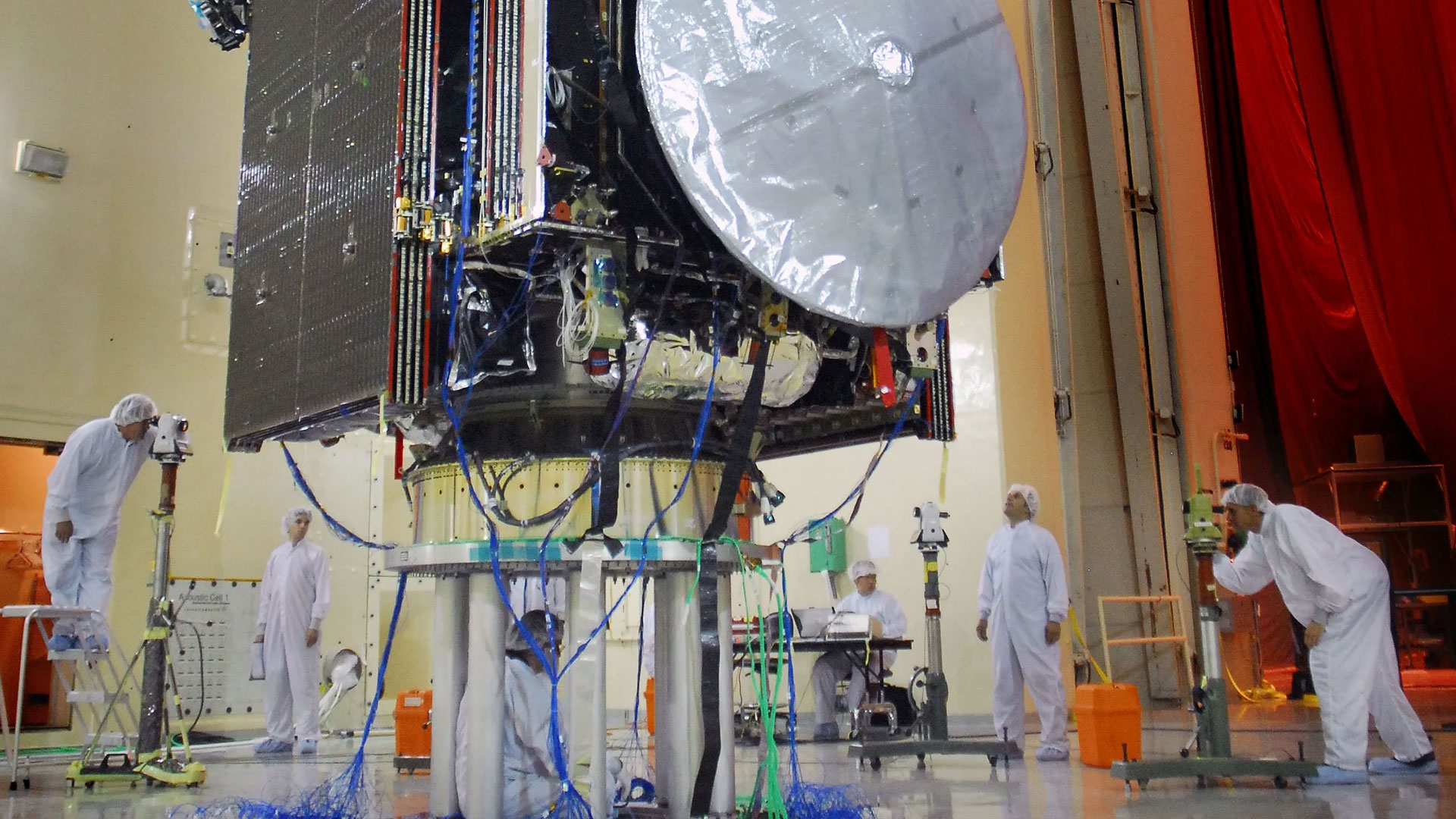
In the realm of aircraft and spacecraft, tiny, hard-to-detect flaws and even the smallest oversights can lead to catastrophic outcomes. Our history of space travel in particular is filled with stories of the people on every level from astronauts to ground control putting in heroic efforts to salvage lives in the face of impending disaster, from Apollo 13 to Soyuz MS-10. The malfunction and near loss of the Advanced Extremely High Frequency satellite (AEHF-1) in 2010 due to a tiny piece of cloth in the wrong place is not quite so dramatic, but underscores just how important it is that forms of nondestructive testing (NDT) such as neutron radiography, which can find tiny flaws that other NDT methods might miss, are more accessible to aerospace manufacturers.
What Nearly Brought Down AEHF-1?
AEHF-1 was a communications satellite commissioned by the US Air Force as part of the Pentagon’s efforts to expand its communications infrastructure to better handle fast, high-bandwidth exchanges of ever-growing vast amounts of data from across the world and constructed by Lockheed-Martin.
The launch went smoothly and the satellite settled easily into its place in Earth’s orbit—seven tons of human ingenuity sailing 140 miles overhead. Everything seemed to be perfectly functional… for about a day. The next day, AEHF-1’s controllers set their minds to remote controlling its engine to transition its flight path from an elliptical orbit around the Earth to a stable geosynchronous orbit that would allow it to remain fixed overhead in perfect harmony with the turning of the Earth along its axis.
But the engine didn’t work. Repeated attempts to fire the engine failed, risking the destruction of the satellite. While every other system onboard the satellite worked perfectly, AEHF-1 was useless in its current orbit: merely a two billion dollar paperweight circling the Earth. And worse, the elliptical orbit it was in would slowly decay over time; if nothing could be done to correct its position, it would fall into Earth’s atmosphere and likely destroy itself upon reentry.
It was up to the engineers at the Pentagon’s Space and Missile Systems Center to somehow salvage AEHF-1. It took a week of nonstop work with not a single engineer leaving the center—they had to order pizzas and have them shoved under the door for sustenance*—until they had a solution. In addition to its main engine, AEHF-1 had small thrusters all around it which were to be used for small course corrections.
They were not going to be used for small course corrections.
Instead, they were going to shift the satellite’s orbit by thousands of miles until it reached its intended path through a long, painstakingly planned-out series of tiny course corrections. As the old saying goes, the journey of a couple thousand miles begins with a single course correction. Fourteen months later, AEHF-1 was in position and working as intended. Over the course of those fourteen months, the engineers had to deal with new issues that cropped up, including heightened risks of overheating, running out of fuel, and colliding with other satellites as it crossed their paths on its long, slow journey. But eventually, everything clicked into place. The satellite was saved and ready to begin its work.
All of this chaos stemmed from the tiniest of flaws—a little piece of cotton had been trapped in a fuel line during the manufacturing process and had escaped the notice of Lockheed-Martin’s quality control. During the manufacturing process for these types of fuel lines, cotton balls are shoved down the pipes in order to collect stray metal shavings left over from machining. Somehow, the cotton ball was not removed and was sealed into the component, remaining in place when the satellite was launched unbeknownst to the manufacturers and engineers.
*They must have been thin crust pizzas.
A New Perspective with Neutron Vision
In hindsight, a tiny bit of cloth caught inside a fuel line is, while a rare occurrence, a frighteningly easy thing to miss. With the component already manufactured, most forms of quality assurance that would have caught it would have involved disassembling it or destroying it; if destructive testing methods were employed, spot testing likely could have missed this part.
Most radiographic methods typically used for nondestructive testing which allow you to catch flaws dwelling deep within a part without dismantling or destroying it, such as X-ray or gamma ray imaging, would not have found the problem either. X-rays and gamma rays are forms of penetrating radiation that pass more easily through light materials than dense materials, and tend to have difficulty penetrating metals such as aluminum or lead. You can increase the energy of the radiation to allow it to pass through denser material, but as a consequence, the radiation will pass even more easily through lighter materials without capturing sufficient details on film. For this reason, industrial X-ray and gamma ray imaging typically fall short in situations involving a light material (such as cloth) within a part constructed from denser material (such as a metal pipe meant for transporting fuel).
However, one certain form of industrial radiography is perfect for such situations. Neutron radiography, or N-ray, has very different attenuation properties than other forms of penetrating radiation. For starters, the way neutrons interact with materials doesn’t depend on density, so there are a lot of dense materials—aluminum, lead, and many other metals—that easily permit neutrons to pass through and many light materials—especially hydrogen-rich and organic materials—that do not. For this reason, N-ray is a particularly useful tool for examining the presence of light materials within dense shells. For example, N-ray can more easily detect the presence of o-rings, seals, water, or lubricants in complex metal assemblies, or plastic materials surrounded by metal objects.
And as for a tiny bit of cloth trapped in a fuel line…
Inspired by the story of AEHF-1, our engineers arranged a test by taking a radiographic image of an aluminum pipe with a cotton ball stuffed in it. While not a one-to-one recreation of the tiny flaw that turned what would have been a simple and problem-free launch into a fourteen-month ordeal, it illustrates the same general concept:

Predictably, our X-ray imaging system was unable to capture the interior of the pipe on film. Aluminum, due to its density, is opaque to X-rays at typical industrial energy levels. Our neutron imaging system, on the other hand, could easily capture the cotton ball within the pipe on film, since more neutron radiation could penetrate the metal than the cotton.
Making N-Ray More Accessible in Aerospace NDT
X-ray vision is a ubiquitous part of the industrial NDT professional’s toolkit, but neutron vision not so much. Due to accessibility issues—there are very few facilities capable of generating high enough neutron fluxes to produce industrial-quality radiographs—N-ray is currently only used in a few niches where it is absolutely necessary.
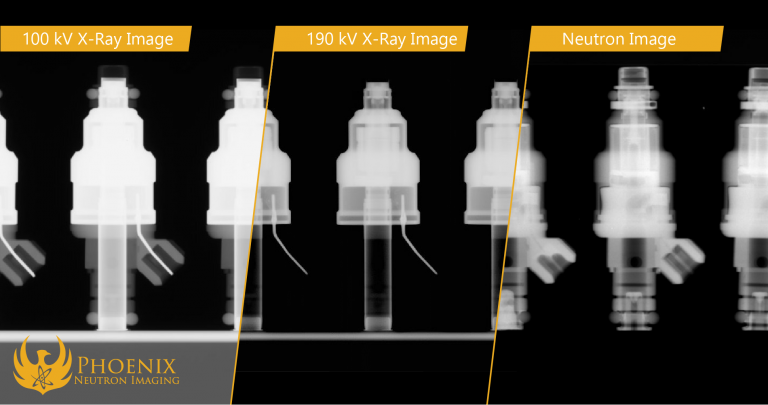
One such example of certain niches in aerospace NDT where neutron radiography is indispensable is in the quality assurance of energetic devices such as the ejection mechanisms in fighter jets and payload fairing separation systems in spacecraft. Energetic devices encase explosive hydrogen and nitrogen-rich compounds within dense metals, which makes them difficult to examine using nondestructive means. Just like the cotton in the fuel line, energetic material can be difficult to capture on film using x-rays, which can make it difficult to spot gaps, cracks, voids, and bubbles in the material that can indicate a disastrous issue. Neutron imaging is the most effective means of ensuring as best as humanly possible that these critical devices will function properly when needed, since as one can imagine, a lot can go wrong very quickly when a fighter jet’s ejection system or a space launcher’s payload release system doesn’t work properly when it’s supposed to.
Phoenix has been working for years to advance nuclear technology, creating compact particle accelerator driven neutron generators that can be used for industrial N-ray in addition to existing neutron imaging facilities, most of which rely on fission reactors for their neutron output. An increase in the number of neutron imaging facilities such as the Phoenix Neutron Imaging Center will improve the availability of N-ray to NDT professionals in the aerospace manufacturing industry. With more plentiful options for neutron imaging, more and more manufacturers of components for aircraft and spacecraft will be able to use this technique in quality assurance to discover some potentially catastrophic flaws that might otherwise escape their watchful eyes.