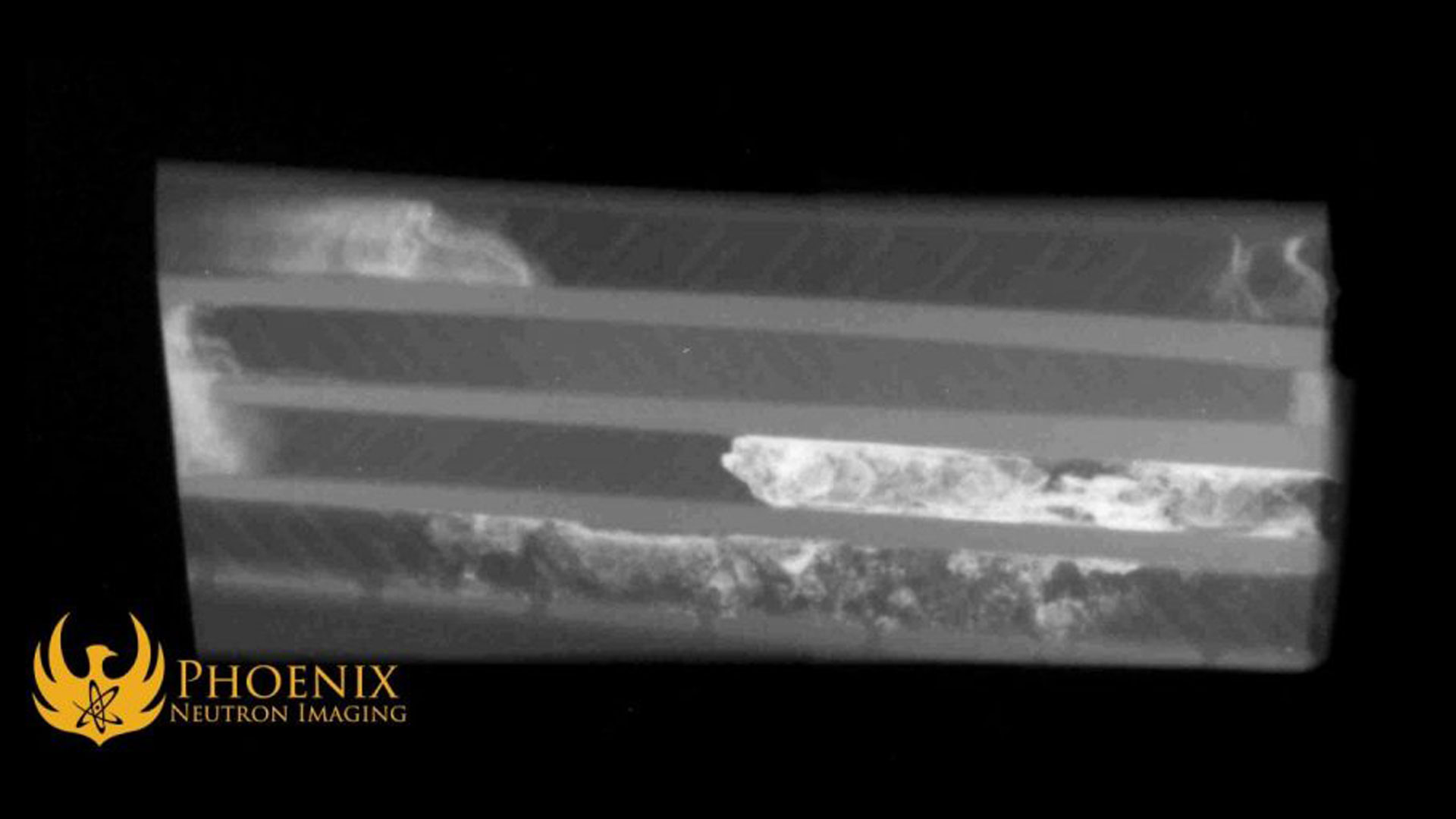
Special thanks to Aaron Craft, R&D Scientist at Idaho National Laboratory and President of the International Society for Neutron Radiography, for his assistance with this article
Neutron absorbent elements, which are defined by their high neutron capture cross sections, are an important element of neutron radiography that can lend the technique a unique edge over other forms of NDT radiography. Such neutron absorbers include boron, indium, and most frequently gadolinium. Gadolinium and other neutron absorbers are extremely opaque to neutron imaging because of their affinity for absorbing neutrons, which make them a powerful tool for many neutron radiography applications, such as the quality assurance of jet engine turbine blades; finding cracks, discontinuities, and stress fractures in manufactured parts; and inspecting spent nuclear fuel rods.
Contrast Tagging in Neutron Radiography NDT
One of the most useful applications of gadolinium in neutron radiography is in the inspection of the turbine blades used in jet engines. Turbine blades are cast around ceramic molds out of light metals that have melting points lower than the temperatures of their operational environments, and so they must be cast with air-cooling channels that prevent them from breaking or melting in use. If fragments of the ceramic core remain embedded in a blade’s cooling channels, the blade will fail and risk serious damage to the aircraft and harm to its pilot and passengers.
Neutron absorbers play a critical role in helping turbine blade manufacturers root out these flaws. In both neutron radiography and X-ray radiography, the light metal of the turbine blades and the ceramic fragments have similar cross-sections, which means the contrast between them cannot be easily distinguished. However, because gadolinium is opaque to neutron radiation, gadolinium-rich areas on a neutron image show up as extremely noticeable bright spots, and gadolinium can be used to “tag” the ceramic present within a turbine blade and make it clearly visible on a neutron image.
To perform gadolinium contrast tagging for neutron imaging, the parts to be imaged are washed with a suspension of gadolinium particles in water or alcohol, then left to sit for a few minutes before being rinsed clean. While the part sits, the gadolinium solution seeps into the porous structure of the ceramic fragments and remains there even after the rest of the gadolinium has been washed away. When the part is imaged, the gadolinium-rich ceramic fragments show up in stark contrast to the surrounding material.
Gadolinium tagging makes neutron radiography an indispensable quality assurance method for turbine blade manufacturers, as it is the most reliable way to detect these dangerous flaws that can crop up in their product. Therefore, turbine blade manufacturers depend heavily on neutron radiography vendors to root out these issues as thoroughly as humanly possible. A large volume of the radiography work done at the Phoenix Neutron Imaging Center (PNIC) comes from turbine blade manufacturers.
Since this application of gadolinium tagging relies primarily on the porous, spongy makeup of ceramic materials, its use cases are limited in scope to a few niche products such as turbine blades and other parts that are cast in ceramic molds. It is a powerful tool for nondestructive testing, but one with very specific uses.
Combining N-Ray and Liquid Penetrant NDT with Gadolinium
There is another interesting way to use gadolinium in conjunction with neutron imaging. This one use case, which our engineers are currently investigating, relies on marrying neutron imaging with another nondestructive testing method: liquid penetrant testing.
Liquid or dye penetrant testing is a form of nondestructive testing in which the surface of a part is washed with a liquid dye. If there are any cracks or pores on the surface, capillary action draws the liquid into them. Using a dye penetrant test, nondestructive inspection professionals can find superficial flaws and discontinuities in a part by visually inspecting where the dye settles and where it remains after the rest of the part’s surface has been wiped clean.
The same technique can be paired with neutron imaging to to peer even deeper into a part. By using a more concentrated gadolinium solution, we can rely on capillary action to trap gadolinium into the cracks, voids, and discontinuities in a material the same way we rely on the porous nature of ceramic to find dangerous flaws in jet engine turbine blades. Just like the turbine blades, the subsequent neutron image we take shows these flaws in stark contrast to the surrounding material.
So far, we can see some clear advantages to gadolinium penetrant neutron imaging compared to liquid penetrant testing on its own. A standard superficial dye test shows you the location and extent of a crack on the surface of a part, but a neutron image gives you a deeper look into the part and can tell you even more about the location and extent of the damage.
Our first test of this method was on a cracked aluminum bar, and our results have been very promising so far: the gadolinium tagging makes it far easier to see where the crack is and how deeply it penetrates the aluminum compared to a neutron image on its own. Our engineers are still experimenting with defects of various sizes to see how effectively gadolinium penetrant testing can bring new insights to our neutron imaging techniques.
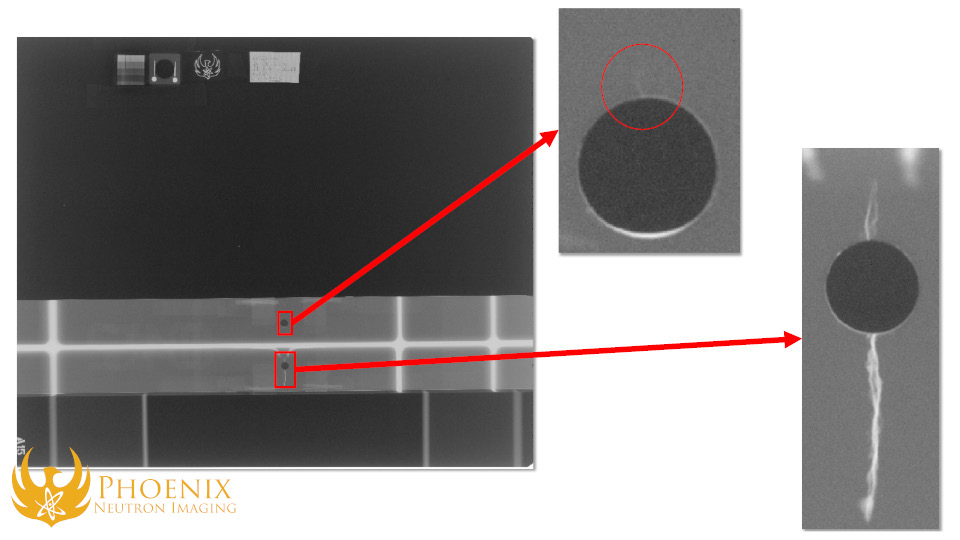
One concern to keep in mind is gadolinium’s opacity compared to the surrounding material. The usefulness of gadolinium in neutron imaging is derived from its capacity and willingness to absorb neutrons, which is what makes it opaque on neutron images. This makes it an excellent contrast agent to use on parts comprised of materials with low rates of neutron attenuation such as aluminum, but materials such as plastic that are very opaque to neutrons already, or very thick materials that require higher energy neutrons to penetrate lessen the usefulness of gadolinium tagging. Therefore, just like with turbine blades, this form of nondestructive testing has specific and niche use cases.
Our engineers have currently only experimented with gadolinium penetrant testing with two-dimensional, planar neutron imaging, but we are also investigating its usefulness in computed tomography, which takes neutron images from multiple angles and constructs them into a three-dimensional model. This could prove far more useful in showing the presence, position, and extent of cracks and other discontinuities in certain parts than a single planar image.
Using Gadolinium to Neutron Image Nuclear Fuel
Inside every fission reactor are a set of fuel rods: long, thin, hollow zircaloy tubes filled with uranium pellets. Because uranium is so reactive to neutrons, neutrons play a key role in the inspection of nuclear fuel, but there are several different methods in which neutrons can be used for fuel assay depending on the circumstances.
New fuel rods fresh out of the factory are typically examined using an intermediate-yield neutron source, such as the neutron-emitting synthetic isotope californium-252. The rods pass through an irradiation chamber which bombards them with neutrons and causes them to emit gamma radiation. The gamma radiation is then picked up by a sensor, and the patterns produced allow the fuel scanning system to determine the enrichment levels of the uranium pellets within each rod. Phoenix’s nuclear fuel scanning system follows this process, albeit with one of our deuterium-deuterium neutron generators standing in for californium-252. This process is critical for quality assurance; every single fuel rod produced has to go through it before being put to work.
For fuel rods that have been in use for a while or that have reached the end of their lives, nondestructive inspection can be useful in determining how well or poorly they have aged as a result of their burdens. A twelve-foot-long uranium fuel rod, on average, lasts about six years until the fissile uranium inside has been used up. Spot testing fuel rods during their operational lifetime or at their end of life helps nuclear engineers discover how the rods break down and can be used to design better fuel rods or bring attention to ways the manufacturing process can be improved.
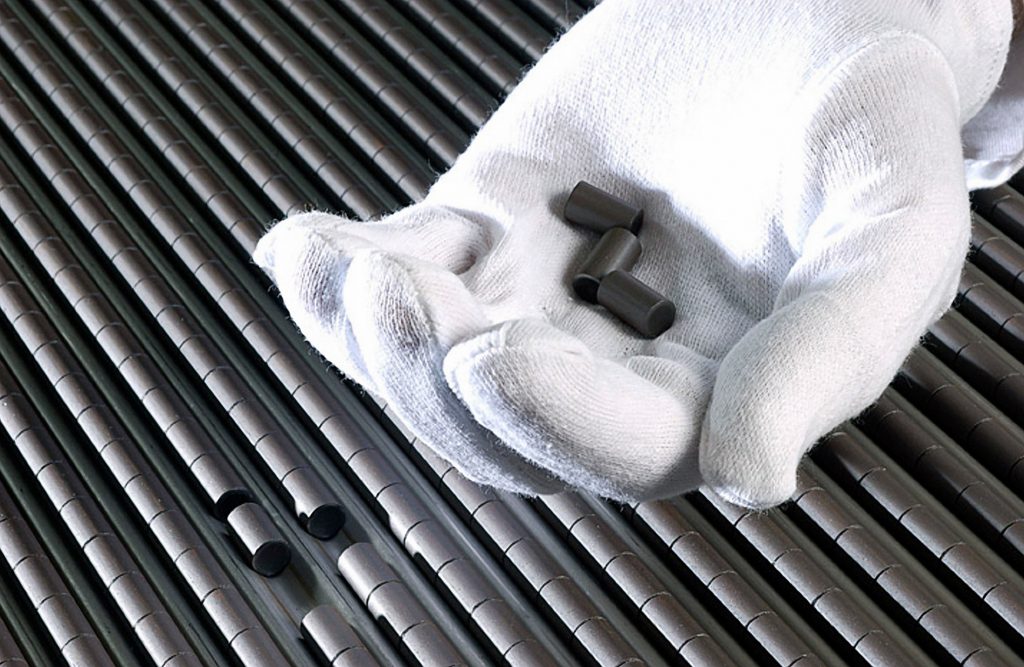
Unlike nuclear fuel rods fresh from a factory, fuel rods that have been used in a nuclear reactor are highly radioactive from the years they’ve spent in the reactor, so a different method is required to inspect the uranium pellets within them for flaws. Because these rods emit more than enough gamma radiation to ruin any film, an indirect “transfer” method of neutron imaging must be employed in which the rod is examined using a neutron absorbent foil instead of film. The foil is insensitive to gamma radiation but becomes activated by a neutron beam passing through the used fuel rod, and the activated foil is subsequently processed to produce a radiographic image.
The Idaho National Laboratory, or INL, is one of the only nuclear research facilities in the world built from the ground up with the shielding, infrastructure, and security to handle the inspection of spent fuel rods, experimental forms of nuclear fuel, and other such objects. INL’s researchers have recently made great strides in using gadolinium to assist in neutron-driven computed tomography, which constructs three-dimensional models of objects out of many two-dimensional neutron images.
In a recent experiment testing digital neutron imaging systems in a high-radiation environment, researchers at INL used N-ray to inspect a gadolinium-tagged prismatic fuel element used in high-temperature gas-cooled nuclear reactors for defects. This was primarily a test of INL’s digital neutron imaging capabilities, but also demonstrates the usefulness of gadolinium in finding cracks, voids, and discontinuities in parts under certain conditions. In the 3D rendering produced by the collected neutron images, the area where the gadolinium penetrant had collected within the fuel element—a crack or porous defect in the part’s composition—is highly visible to the naked eye.
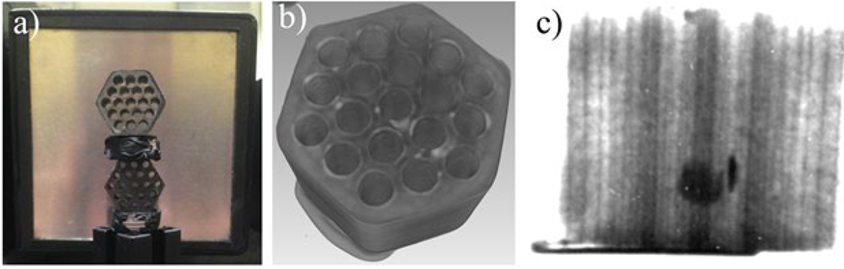
Gadolinium has the highest absorption cross-section of any element, and Gd-157 in particular. Even a little bit of this material provides high contrast. We are exploring gadolinium-containing liquid penetrants for enhancing the visibility of cracks and open porosity of materials including nuclear fuels. Some small cracks and open porosity can be difficult, if not impossible, to visualize using neutron imaging. However, the introduction of a contrast agent such as gadolinium can make the smallest and most invisible features stand out.
Aaron Craft
R&D Scientist, Idaho National Laboratory; President, International Society for Neutron Radiography
While the use of gadolinium and other neutron absorbers in conjunction with N-ray for contrast tagging and indirect imaging may have applications in only a few niches, these niche applications are both critically important and downright fascinating in their own rights. As materials science and nuclear technology advance, we’re sure that nuclear researchers, the NDT community, and neutron imaging vendors will keep inventing new methods and applications to take advantage of the unique capabilities that neutrons can offer.