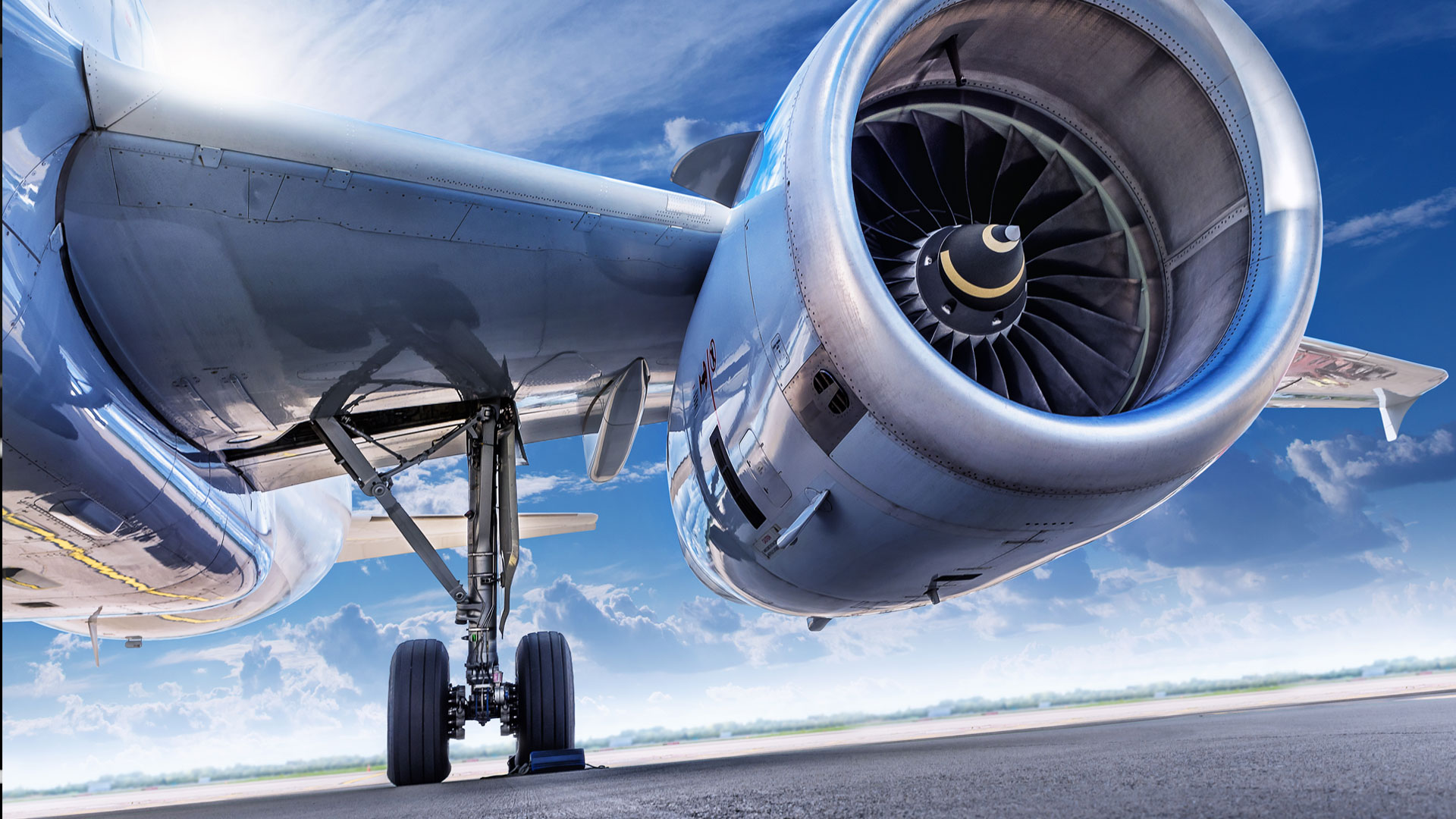
X-ray and industrial computed tomography are powerful and commonly used techniques in any materials testing laboratory, but components with dense materials forming their outer layers can prove difficult to analyze through these methods alone. Neutron radiography, on the other hand, penetrates dense materials easily to create detailed images of their inner workings, making it essential for comprehensive radiographic testing.
Neutron imaging is a powerful tool for NDT materials testing applications related to:
- Composite materials and polymers development
- Lab testing for prototypes
- Materials failure analysis and QA
- Weld integrity tests
- Concrete inspection
- Radiation hardening and survivability testing
- Energetic materials testing
- Nuclear fuel testing and inspection
Below, we’ll explore a few of these powerful applications in greater detail.
Rapid Prototyping
Before the advent of industrial 3D printing and additive manufacturing, prototyping was a lengthy process. New technology allows prototypes to be made quickly and easily, reducing the time it takes to develop new products and encouraging experimentation.
Before a prototype can become a full-fledged product, extensive materials testing is required to sort out any issues with the design. Neutron imaging is a useful method for detecting issues with 3D-printed material, especially composite materials.
Failure Analysis
Due to a current lack of accessibility to powerful neutron sources, neutron imaging is seldom used for comprehensive quality assurance outside of a few industrial niches, but plays an important role in failure analysis.
When products fail, manufacturers must turn to comprehensive materials testing to determine if any flaws were overlooked in the product’s design or if any unforeseen issues have cropped up over the course of the product’s lifespan.
One aspect of neutron radiography that makes it such a powerful method for materials testing and failure analysis is the way certain elements, such as gadolinium, react to it. By “tagging” an object with liquid gadolinium, which has a high neutron cross section, flaws in the object such as corrosion, cracks, and other failures that might otherwise be difficult or impossible to see will show up in stark contrast on the neutron image.
Weld Analysis
In an object with two or more parts welded together, the connecting points undergo a lot of stress and fatigue. If the welds holding the object together are not sound, the object could break apart under the strain. Materials inspection, both by destructive and nondestructive methods, is crucial to ascertain that the welds in an object are strong enough to stand up to the demands of use.
Radiographic testing is a powerful method for weld inspection and analysis, and the unique properties of neutron radiation and the high boron content in welding flux allow neutron imaging to pick up crucial details that might otherwise be missed.
Concrete Inspection
There are a wide variety of materials testing methods, nondestructive and otherwise, that are applied to concrete testing and inspection. The strength and integrity of concrete can be difficult to test through common means of materials testing due to its heterogeneous makeup.
Radiography and neutron activation analysis can effectively measure density and detect some structural flaws in concrete. Among the several types of radiography, neutron radiation’s unique properties over X-ray and gamma rays make it a useful tool for concrete inspection.
Energetics/Pyrotechnics Inspection and Detection
Neutron radiography is particularly useful when inspecting energetic and explosive devices from airbag inflators and explosive signal transmission systems to bombs and munitions. These devices consist of a dense metal shell encasing a chemical propellant. While the density of the outer layer proves problematic to other forms of industrial radiography, neutrons pass through the metal to create an image of the chemical within.
If the chemical propellant undergoes any unexpected changes in its makeup, its behavior could become unpredictable. Issues with the chemical makeup of an energetic device’s propellant show up as bubbles, cracks, voids, or other anomalies within the material. A neutron image can show these anomalies, while X-rays cannot.
Radiation Hardening and Survivability Testing
In the aerospace industry, many components, especially electronics, must be specially designed to experience high-radiation environments such as space. Neutrons are especially useful for this area of materials testing. Bombarding components with neutrons simulates these environmental conditions and allows manufacturers to gauge how well their products meet their requirements when used in spacecraft and satellites.
Nuclear Fuel Inspection
Uranium fuel rods used in nuclear reactors must conform to strict quality standards before being put to use. A fuel rod contains pellets of fissile uranium. The distribution of uranium within the rod must be uniform, otherwise the rod could behave erratically within the reactor. Of course, not everything that comes off an assembly line comes out perfect, so thorough testing for any broken or misshapen pellets is vital.
While nuclear fuel rods cannot be imaged via the exact same methods as other materials, neutrons play an important role in inspecting them due to the way uranium reacts to them. By measuring the excitability of the pellets of uranium within the rods, a neutron-based nuclear fuel inspection system can detect gaps and other issues that would render the rods unsuitable for use.
NonDestructive Testing at Phoenix
We offer both neutron and X-ray radiography and computed tomography out of our state-of-the-art nondestructive testing lab and imaging center. We’re proud to make these services more accessible to manufacturers, engineers, and NDT professionals in industries ranging from aerospace to healthcare, acting as a one-stop solution for all their industrial radiography needs. Contact us to learn how we can help your organization.